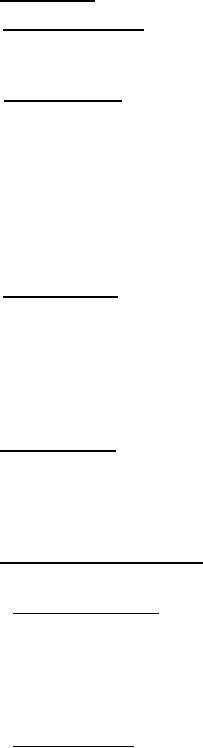
MIL-PRF-32517
4.6.4 Voltage drop. Splices shall be tested as follows (see 3.4.4):
a. Sample preparation. The MIL-DTL-17 cable insulation shall be stripped 2 inches
from both ends. The shield shall be trimmed so exposed length is ¼ inch. Strip ¼ inch of the
primary conductor's insulation.
b. Outer conductor. Measurements shall be made by puncturing the insulation of the
current carrying conductor on each end of the splice ¼ inch back from the ends of the matched
impedance splice. The distance between the 2 test points shall be noted. Measurement of the
current carrying conductor shall be made by puncturing the conductor insulation the same
distance between test points as that noted for the splice measurement. The millivolt drop of the
equivalent length of wire may be determined by averaging 4 readings taken on 10-inch lengths of
wire selected at random throughout the supply of wire to be used for subsequent tests. The
millivolt drop through the crimp termination and the current carrying conductor shall be
measured while 1 ampere direct current (DC) is being applied.
c. Inner conductor. Measurements shall be made by puncturing the insulation of the
current carrying conductor on each end of the splice 3½ inches back from the ends of the
matched impedance splice. The distance between the 2 test points shall be noted. Measurement
of the current carrying conductor shall be made by puncturing the conductor insulation the same
distance between test points as that noted for the splice measurement. The millivolt drop of the
equivalent length of wire may be determined by averaging 4 readings taken on 10 inch lengths of
wire selected at random throughout the supply of wire to be used for subsequent tests.
4.6.5 Tensile strength. Stripped ends of the repaired cable shall be placed in a standard
tensile-testing machine so that the matched impedance splice is centered between and at least 3
inches from the jaws. Sufficient force shall be applied to pull the inner conductor out of the
splice or break the cable or the splice. The travel speed of the head shall be 1 inch per minute.
The clamping surfaces of the jaws may be serrated to provide sufficient force (see 3.4.7).
4.6.6 Environmental conditioning. The matched impedance splices shall be exposed to
each of the conditions in the sequence shown in table VI.
4.6.6.1 Altitude immersion. The installed matched impedance splice shall be immersed
in a water bath and placed in a suitable chamber; the free ends shall be within the chamber and
shall not be sealed (see 4.2.4). The chamber pressure shall be reduced to 75,000 ft. (26.78 mm of
Hg) and maintained for 30 minutes. The chamber shall then be returned to ambient pressure (see
4.2.). This shall constitute 1 cycle. A total of 3 cycles shall be run. The insulation resistance shall
be measured after the third cycle (see 3.4.9).
4.6.6.2 Fluid immersion. The installed matched impedance splice assemblies shall be
immersed in the fluids specified in table XII at the temperature and time period listed. A separate
matched impedance splice assembly shall be immersed in each of the required fluids. All fluid
immersion samples shall be subjected to the subsequent tests (see 3.4.10).
18
For Parts Inquires call Parts Hangar, Inc (727) 493-0744
© Copyright 2015 Integrated Publishing, Inc.
A Service Disabled Veteran Owned Small Business