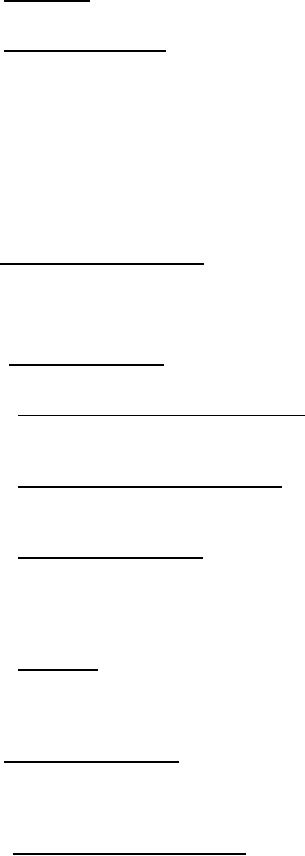
MIL-PRF-32517
3.6 Heat source. The manufacturer's recommended heat convection air, infrared, or
equivalent shall be used.
3.7 Assembly instructions. If specified in the contract (see 6.2), assembly instructions
for each matched impedance splice assembly kit will include:
a. Cable preparation stripping dimensions and tolerances.
b. List and description of crimping, stripping, or special tools if required.
c. Pictorial presentation of subassemblies and loose piece parts.
d. Sufficient pertinent dimensions for verification of correct parts: As a minimum,
the cable entry openings for the conductor, dielectric, braid, and jacket should be specified.
e. Military PIN and manufacturer's PIN (see 1.2).
4. VERIFICATION
4.1 Classification of inspections. The examinations and tests of matched impedance
splice assemblies are classified as follows:
a. Qualification inspection (see 4.3).
b. Conformance inspection (see 4.4).
4.2 Inspection conditions. Unless otherwise specified herein, all inspections shall be
made at ambient temperature and humidity as specified in MIL-STD-202, 4.2 Test conditions.
4.2.1 Test equipment and inspection facilities. Test and measuring equipment and
inspection facilities of sufficient accuracy, and quantity to permit performance of the required
inspection shall be established and maintained by the contractor.
4.2.2 Matched impedance splice assembly. The splices shall be installed on cables
conforming to MIL-DTL-17 by the testing activity using the specified tooling (see 3.3.2). Unless
otherwise specified, the leads shall be at least 5 feet in length (10 feet total length).
4.2.3 Temperature stabilization. Voltage drop measurements shall be made after the
temperature of the matched impedance splice assembly has stabilized. Temperature stabilization
shall be determined by 3 consecutive readings within ±1 °C at intervals of 3 minutes each. All
tests performed after exposure to high or low temperature shall be conducted after splices have
been conditioned for at least 1 hour at the inspection conditions specified (see 4.2).
4.2.4 Water bath. Unless otherwise specified in the applicable test method, a water bath
containing 0.5 percent of an anionic wetting agent (see P-D-410) and 5.0 percent sodium
chloride shall be used whenever immersion is specified. Free ends of coaxial cable shall be a
minimum of 4 inches from top surface of water.
4.3 Qualification inspection. Qualification inspection shall consist of the examinations
and tests in table VI. Unless otherwise specified in table VI, sequential testing is required for
each group. The qualifying activity shall perform or witness the particular tests as specified in
table VI and the supplier shall perform the remaining tests.
4.3.1 Qualification inspection process. At the initiation of the qualification process, prior
to testing, prospective suppliers must forward a written request for qualification to the qualifying
activity (see 6.3). The qualifying activity will respond in writing with a formal "letter of
authorization" providing detailed instructions for the submission of product samples. Testing
cannot begin until the supplier has received this authorization letter. The qualification process is
described in the SD-6 (see 6.3.1).
10
For Parts Inquires call Parts Hangar, Inc (727) 493-0744
© Copyright 2015 Integrated Publishing, Inc.
A Service Disabled Veteran Owned Small Business